線切割放電加工機是一種特種檢測儀(yi) 器,在多個(ge) 工程領域有著廣泛的應用。其通過向電極(通常是金屬絲(si) )施加電壓,使其與(yu) 工件相互靠近,從(cong) 而破壞兩(liang) 者之間的絕緣性,引發放電現象來進行加工的方法。在加工過程中,金屬絲(si) 與(yu) 工件之間的空間被加工液充分填充,當兩(liang) 者之間的距離足夠近時,電流會(hui) 像閃電一樣從(cong) 電極流向工件,產(chan) 生劇烈的放電現象和大量的熱量。這種放電現象會(hui) 持續進行,直至工件被切割開來。加工過程中產(chan) 生的廢料會(hui) 被加工液排出,同時電極與(yu) 工件之間的絕緣性也會(hui) 逐漸恢複。
1、操作前準備
設備檢查:確認設備接地良好,各部件連接牢固,無鬆動或損壞現象。檢查電極絲(si) 的安裝是否正確,餘(yu) 量是否滿足加工需求,並檢查其是否有破損或纏繞等情況。同時,查看加工液的液位、比電阻值是否正常,確保加工液循環係統暢通無阻。
工件準備:根據加工要求,選擇合適的工件材料,並將其表麵清理幹淨,去除油汙、雜質等。使用合適的工裝夾具將工件固定在機床工作台上,確保工件的位置準確、牢固,且不會(hui) 在加工過程中發生位移或振動。
參數設置:根據工件的材料、厚度、形狀以及加工精度要求等,在設備控製係統中設置相應的加工參數,如脈衝(chong) 電壓、脈衝(chong) 電流、脈衝(chong) 寬度、脈衝(chong) 間隔、進給速度、放電間隙等。這些參數的合理選擇直接影響加工效率和質量。
2、加工操作過程
開機與(yu) 尋原點:打開設備電源開關(guan) ,啟動機床。在控製係統中選擇“尋機械原點”功能,使機床的坐標軸自動回到初始位置,建立準確的坐標係,以確保加工精度。
導入加工軌跡:根據工件的加工要求,使用專(zhuan) 業(ye) 的編程軟件繪製加工軌跡,並將其生成的代碼或圖形文件導入到線切割放電加工機的控製係統中。常見的編程軟件有AutoCAD等,可通過特定的接口或數據傳(chuan) 輸方式將軌跡信息傳(chuan) 輸給設備。
定位與(yu) 對刀:移動機床的工作台和電極絲(si) ,使電極絲(si) 與(yu) 工件的起始加工位置對齊。可以通過手動操作或使用自動對刀功能來完成這一步驟,確保電極絲(si) 與(yu) 工件之間的距離準確無誤,避免因定位不準確而導致的加工誤差或斷絲(si) 等問題。
開始加工:設置好加工參數和加工軌跡後,先啟動冷卻係統,使加工液充分循環,然後開啟放電加工功能。在加工過程中,密切觀察設備的運行狀態,包括電極絲(si) 的張力、放電狀態、加工液的流量和溫度等,確保加工過程穩定進行。同時,注意聆聽設備的運行聲音,如有異常應及時停機檢查。
實時監控與(yu) 調整:通過設備的顯示屏或控製係統軟件,實時監測加工過程中的各項參數和數據,如坐標位置、放電間隙、加工速度等。根據實際加工情況,適時調整加工參數,以優(you) 化加工效果。例如,如果發現加工速度過快導致放電不穩定,可以適當降低進給速度;如果加工精度不符合要求,可以調整放電間隙或脈衝(chong) 參數等。
3、加工完成後操作
關(guan) 機:加工完成後,先將進給速度降至z低,關(guan) 閉放電加工功能,待電極絲(si) 停止運動後,再關(guan) 閉冷卻係統和設備的電源開關(guan) 。按照設備的關(guan) 機流程,逐步退出操作係統,確保設備安全關(guan) 機。
工件處理:將加工好的工件從(cong) 工作台上卸下,清除工件表麵的附著物和加工屑,檢查工件的加工質量是否符合要求。如有必要,可以進行進一步的清洗、打磨或其他後處理工序。
設備清潔與(yu) 維護:清理機床工作台上的切屑、油汙等雜物,保持工作區域的整潔。檢查電極絲(si) 的使用情況,如剩餘(yu) 長度、磨損程度等,及時更換電極絲(si) 。對設備進行全麵的檢查和維護,包括潤滑部件、檢查電氣係統、校準坐標等,確保設備處於(yu) 良好的運行狀態,為(wei) 下一次加工做好準備。
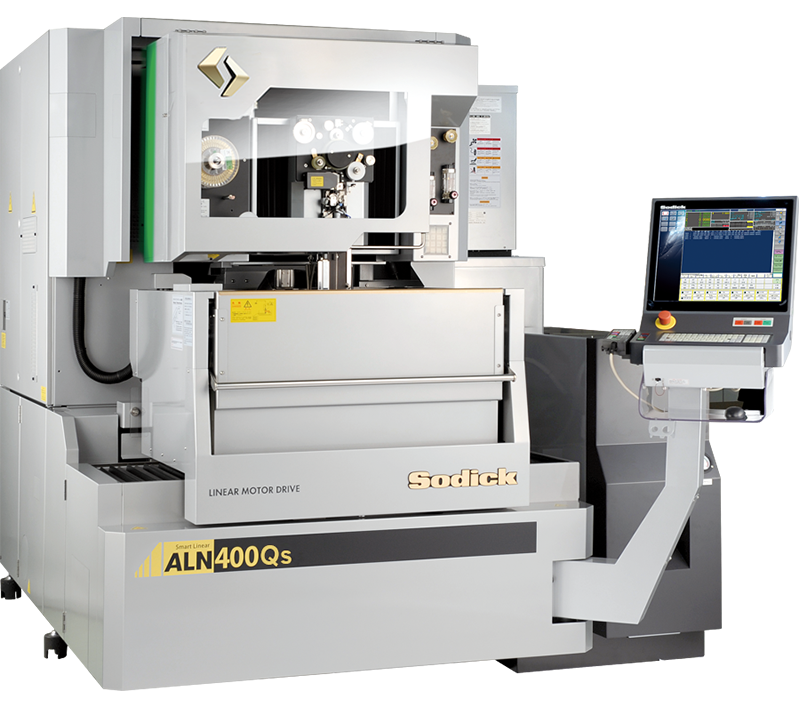